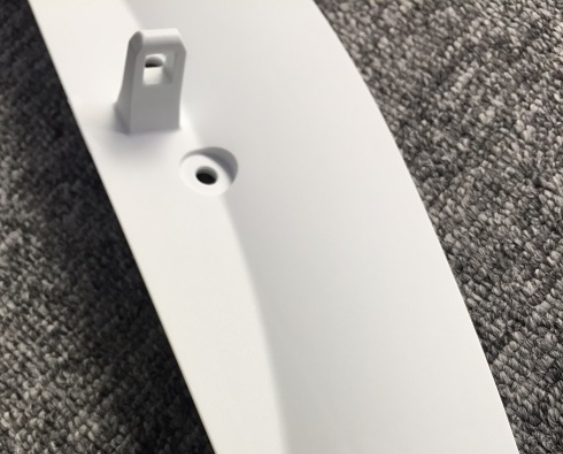
Plastic injection mold is the most widely used mold among all plastic molds, which can form complex and high-precision plastic products. This article is just a rough introduction.
Since it is a chain structure, the shrinkage direction of plastics during processing is also related to the orientation and cooling shrinkage of polymer molecular chains under stress. The shrinkage in the flow direction is more than that in the vertical direction.
Product shrinkage is also related to product shape, gate, thermal expansion and cold shrinkage, temperature, pressure holding time and internal stress. Generally, the shrinkage rate provided in the book has a wide range. In practical application, we consider the wall thickness and structure of the product and determine the size and orientation of temperature and pressure during injection molding. If there is no core support for general products, the shrinkage should be larger. Plastic injection mold is basically divided into static mold and dynamic mold.
The mold with gate sleeve on one side of the injection head of the injection molding machine is a static mold. The static mold is generally composed of gate sleeve, backup plate and template. A simple mold (especially a mold without a core) can also use a thicker template without using the backup plate. The gate sleeve is generally a standard part, and it is not recommended to cancel it unless for special reasons.
The use of gate sleeve is conducive to the installation of mold and convenient replacement without polishing by yourself. Some special mold gate sleeves can be drilled out or cut with taper line. When some molds must be demoulded by static mold, a static mold demoulding mechanism must be added. The structure of moving die is generally moving die, moving die backup plate, demoulding mechanism, die foot and installation fixing plate.
The gate is directly related to the beauty of plastic parts. If the gate design is not good, it is easy to produce defects. It is easy to produce serpentine flow without any obstruction. For products with high requirements, overflow and exhaust shall also be designed. As for the overflow rod, it can not be used on the top of the formwork, which will not affect the service life of the formwork.